Location, location, location.
The owners of Vidimos Inc., a SMACNA member in East Chicago, Indiana, know the old real estate adage also applies to the business of custom steel fabrication. Scott Vidimos, president of the family business, can look out his back door and see a Northwest Indiana industrial landscape where more steel is produced than anywhere else in the U.S. Vidimos Inc. has operated within this steel territory since the early 1970s. They have no more room for expansion, but Vidimos also has no intention of relocating.
“We are in a wonderful location for shipping large pieces locally, including into two of the large, integrated steel mills in the area.” he said. “Although it wouldn’t be easy, we can also ship by rail or barge. There are also a tremendous number of manufacturing plants with whom we’ve built lasting relationships.”
The benefits of having industrial customers as neighbors was clearly visible in early September 2021, when Vidimos Inc. loaded three huge steel fabrications onto truck trailers for a local delivery. The cylindrical pieces are three parts of a replacement tank-shaped receiving hopper that will be used to process valuable slag — a byproduct of iron production. The largest section was 28’-2” in diameter, and 20’-2” high. The loaded weight was 122,000 pounds. The three hopper tank pieces were shipped approximately one mile to a nearby steelmaking facility where the slag is being processed.
Even though the tank only traveled a mile to its destination, arrangements had to be made to move loads that were oversize and overweight. The loads, which protruded 10’ off both sides of the trailer, were obstructed by overhead signs and power lines, and required special routing due to their weight. The loads were accompanied by escorts, bucket trucks, and a crane to clear the obstructions. “Although the shipments were tedious, there is not another local fabricator better situated for a job of this magnitude.”
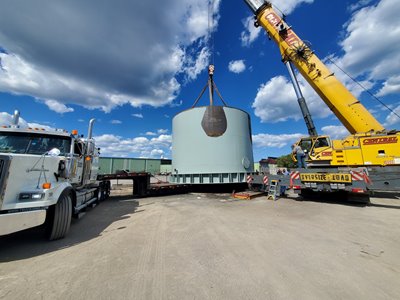
Top conical section and middle cylindrical section staged outside plant awaiting escorts to move pieces inside plant.
For the project, Vidimos Inc. fabricated the tank for Paul Wurth Inc., which provided an improved structural and process design, including accommodation for high temperature service. While slag is incredibly hot when it is cast from a blast furnace, a large volume of water is added to the slag to rapidly cool it down before it reaches the receiving hopper. The granulated slag slurry is rerouted from the hopper to dewatering drums, and then conveyed out to a storage area.
“The granulated slag is a valuable green product for cement companies,” said David Berdusco, VP of Business Development for Paul Wurth, the company that designed the receiving hopper and hired Vidimos Inc. “It has similar chemistry to Portland Cement and it can be ground and used as a replacement for Portland Cement.”
Vidimos Inc. was contracted in early May 2021 to fabricate the 51’ tall hopper tank from 5/8”, 7/8”, 1”, and 1-1/2” steel plate including internal deflectors and drain trough. “We burned the plates on our 10’x40’ high-definition plasma table. The cylindrical sections were rolled on a 1”x10’ plate roll,” Vidimos added. “Beams with holes were processed on our beam line. The pieces were assembled using 10- and 15-ton overhead cranes in the shop and our 20-ton crane outside in our yard.”
The assembly interior and exterior were sandblasted and painted. A significant portion of the lower area received shop welded refractory anchors and hex mesh to accommodate refractory, which is being field installed by the installing contractor. Hot dip galvanized access platforms and ladders were also fabricated and shipped loose.
Vidimos said the size and weight of the three sections were the most challenging aspects of the job. “We fabricated much of the work inside our shop,” he said. “Although the overhead door in the shop is 24’ wide by 20’ high, a portion of the wall had to be removed to move the fabrications into our outside yard for final assembly. At 31,000, 40,000, and 122,000 pounds, we contracted to have a 200-ton crane in to load the pieces for shipment.”
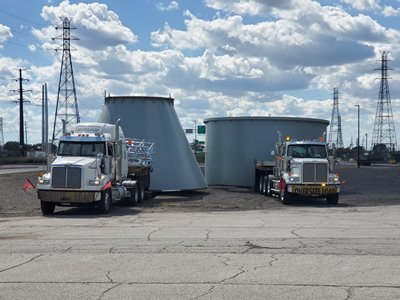
Top conical section and middle cylindrical section staged outside plant awaiting escorts to move pieces inside plant.
With just a four-month timeline, Vidimos scheduled two fabrication shifts to get the project done for on-time delivery. “The ingenuity, dedication, and hard work of our day and night shifts is extremely gratifying,” Vidimos said. “Fabrications of this relative size occur infrequently, but the experience of our craftsmen allows us to ramp up when the need arises.”
Vidimos Inc. has completed other large fabrications at its job shop. “We have shipped stacks, fabricated beams, and assembled conveyor galleries as long as 110’,” Vidimos said. “When the customer’s plant was originally built, we fabricated a 12’-6” diameter stack that shipped 24’ high, which is actually taller than any of the pieces on the tank.”
The family-owned company was founded 75 years ago by Scott Vidimos’ grandfather, who focused on residential HVAC duct fabrication. Twenty years later, steel mill work accounted for more than 50% of the company’s work. Today, steel mill projects account for a maximum of 20-25 percent of their business. The rest is light steel fabrication, duct collection and industrial ventilation systems, as well as maintenance and repair work.
“Steel spending is cyclical,” Vidimos said. “Although our capabilities fit steel mill work, they also suit us well for our other industrial customers.”
With such deep roots in the East Chicago community, the Vidimos family is planning on many more years of business success. In fact, Scott Vidimos' son Adam started working at the family business in 2004. Today he is vice president — a fourth generation Vidimos who will continue partnering with SMART Local 20 to serve their industrial neighbors/customers.